News and Stories
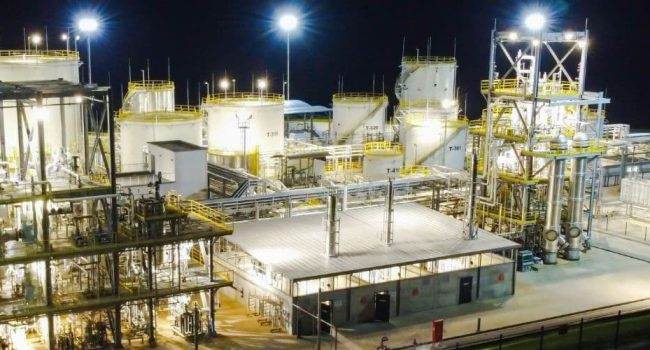
Osmaneli, Turkey
Sequoia's 60000 metric tons re-refining plant deployed in Osmaneli Turkey.
Sequoia is pleased to announce successful start-up of a re-refining plant owned by Tayras, near Osmaneli Turkey. With rated capacity to process 60000 metric tons of waste oil per year, the plant produces stable water while lube base oil exceeding API Group III specification, even though the plant was nominally designed for Group 2 base oil production. Sequoia designed and supplied all the process equipment, instruments, controls and piping components for vacuum distillation and hydrogenation processes.
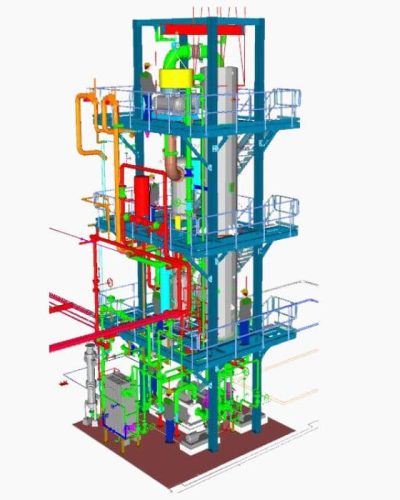
Nevada, United States
Wastewater Treatment Plant using Vapor Compression is operational
Sequoia is pleased to announce successful start of a new wastewater processing plant which uses vapor compression technique. Vapor compression is an energy-efficient way of evaporating water. At a plant in western USA, more than 20,000 gallon (75000 liters) of wastewater is processed every day, yielding more than 75% distilled water, thereby concentrating the wastewater to less than 1/4th of its volume. Wastewater is from a refinery and contains toxic organics, sulfides, phenols, ethylene glycol and metallic compounds. A distillation step is built into the vapor compression technique to further purify the distilled water vapors of undesirable organic contaminants.
By successfully demonstrating the use of vapor compression distillation, we believe that hard-to-treat wastewater(s) from refining, chemical and power industries can be concentrated efficiently. The concentrate from vapor compression distiller can be further processed with a forced-circulation reboiler or an evaporation pond to achieve zero liquid discharge.
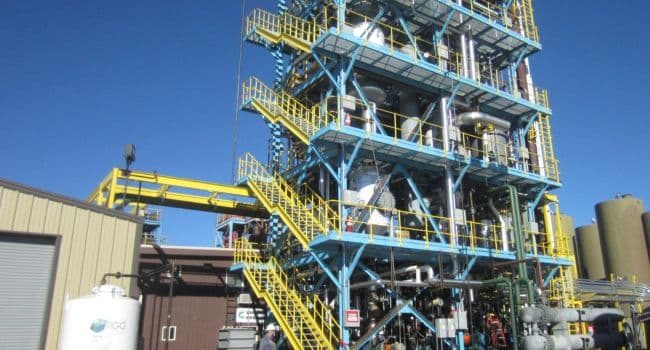
Nevada, United States
Vertical Tube Evaporator (VTE) for used motor oil distillation at Bango Refining
A new vacuum distillation plant for recovery of lube base oil stock form used motor oil was installed at Fallon, Nevada (USA). The new plant uses Sequoia’s proprietary vertical evaporators (WFE). The 70000 gpd (11 m3/hour) plant ran seven months before a heat exchanger or evaporator was cleaned. This is our second US customer using Sequoia’s proprietary design evaporators This plant is operational since January 2013.
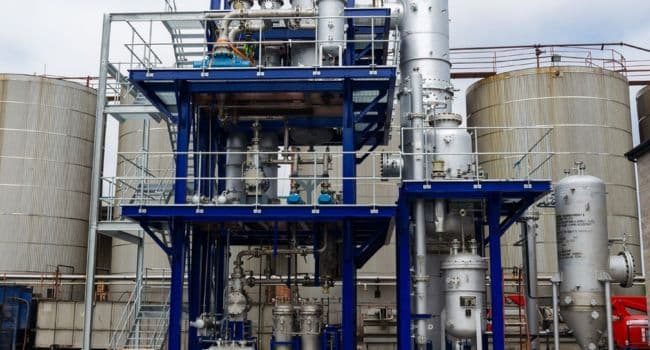
Merseyside, United Kingdom
Sequoia's "Waste Oil to VGO" distillation process operational in the UK
Sequoia’s vacuum distillation process and equipment is now operational in the UK. The plant distills the lube oil fractions from 25000 metric tonnes of waste motor oil per year. Sequoia helped its customer install this plant in a narrow footprint given its port location and also help the customer meet strict environmental permit requirements.
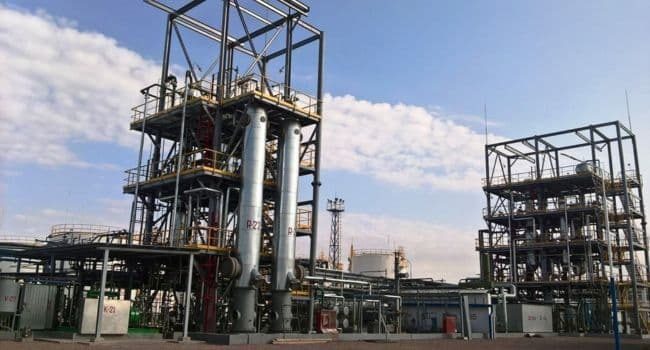
Uzbekistan
Sequoia customer Uz-Prista begins production of Group II base oils
During 2015, Sequoia’s customer Uz-Prista Recycling successfully completed start-up of its vacuum distillation and hydrotreating units for production of Group II base oils from waste lubricating oils. The plant is designed for annual throughput of 45000 metric tonnes of feedstock per year. The products are two grades of water-white base oils. Sequoia believes this is the only complete re-refining plant in the soviet republics including Russia. Sequoia provided the basic design with process license, detailed engineering and also supplied all of the equipment, instruments, controls, pipes, fittings and supporting steel structure for this project. With the completion of this project, Sequoia now boasts operating plants on five continents, in diverse socioeconomic backgrounds.
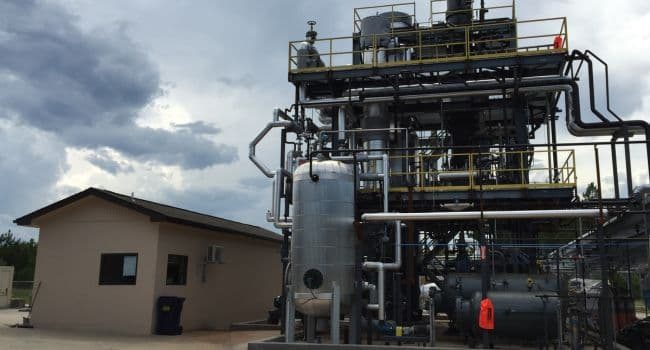
Georgia, United States
Sequoia's semi-batch distillation process launched
Sequoia Energy & Environment designed and supplied a vacuum distillation plant for Synergy Recycling at Kingsland, Georgia (USA). Started in 2015, the plant processes up to 12 million gallon/year of used lubricating oil recovering lubricating oil base stock (LOBS) to be initially sold as vacuum gas oil (VGO). The plant employs Sequoia’s unique distillation process that uses a single distillation column and a single heater to carry out the multi-component separation necessary in the recovery of LOBS. In this project, Sequoia was entrusted with basic design, the detailed design and also the supply of all equipment, structural steel, piping components, instruments and the control panel. Sequoia met all its obligations in a timely manner with the team of its experienced of 25 professionals based in Pune, India. The unique design allows the customer to not only control quality of the distillate product but also control the yield of residual bottoms product between 8-18%, making all options available for sale of the by-product.
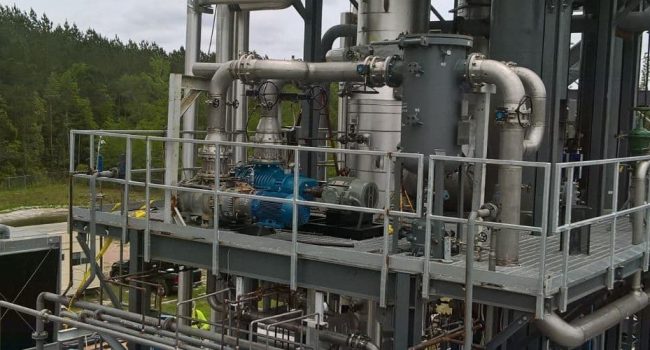
Georgia, United States
Kingsland distillation plant expanded
Sequoia has helped its valued customer in Kingsland, Georgia (USA) expand their VGO plant to more than three times its original capacity. Sequoia supplied additional evaporators with supporting steel, piping materials, instruments and controls. Sequoia also helped install a third-party short-path evaporator for the customer.
By successfully demonstrating the use of vapor compression distillation, we believe that hard-to-treat wastewater(s) from refining, chemical and power industries can be concentrated efficiently. The concentrate from vapor compression distiller can be further processed with a forced-circulation reboiler or an evaporation pond to achieve zero liquid discharge.
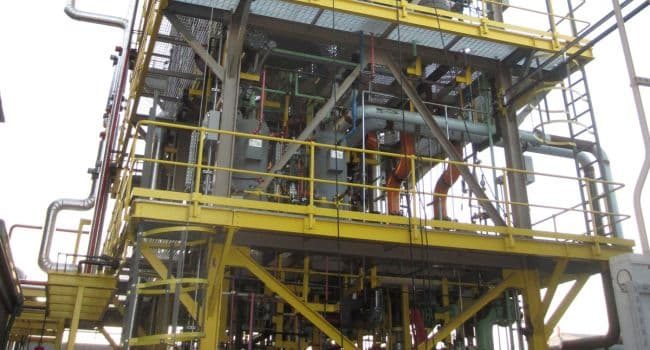
Washington, United States
Marine Diesel Oil (MDO) from waste oil using Vertical Tube Evaporator (VTE)
Sequoia supplied a vacuum distillation plant with its proprietary evaporators to Emerald Recycling at Tacoma, Washington (USA) for processing 50,000 gallon/day (7.5 m3/hour)of used lubricating oil and waste industrial lubricants, making MDO / vacuum gasoil (VGO). With highly reliable and robust rotating equipment and no moving parts in the evaporators, this plant is simple to operate and maintain. Cranes (typical for thin film evaporators) are not required for the maintenance and cleaning of the VT evaporators.
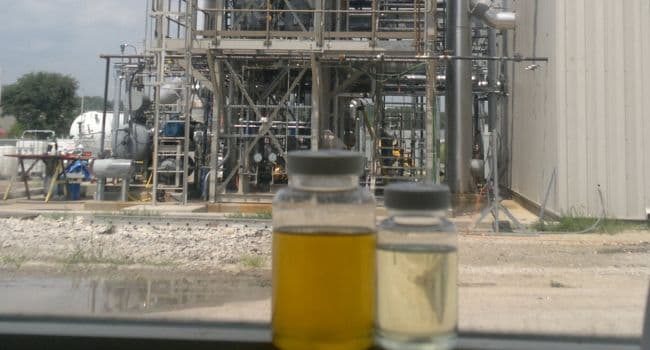
Kansas, United States
Transformer oil recycling by Hydrotreating
Hydrogenation of waste transformer oil (electrical insulating oils) can produce an oil product that is far better in quality and yield in comparison with fixed bed clay adsorption or reaction with sodium metal. This is proven at EMI of KC, a valued client of Sequoia. The 5 million gallon/year throughput naphthenic oil hydrotreater in Kansas City, Kansas (USA) produces oil free of PCBs (polychlorobiphenyls – known carcinogens). The product oil has water-white appearance and low sulphur concentration. Sequoia designed the complete plant, supplied all processing equipment and also supplied a thermal oxidizer for safe disposal of process off-gases from the plant.
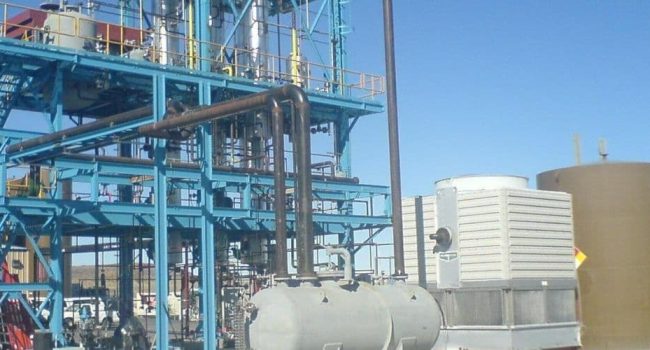
Nevada, United States
Hydrotreater proven at small scale and expanded skillfully
Bango Refining of Fallon, Nevada (USA) was using fixed-bed clay process for upgrading distillates recovered from used oil. The product had poor color, poor oxidation stability and there was no control over reduction of sulfur in the final products. From March 2009, with the Sequoia-supplied hydrotreater, Bango Refining started making Group 2+ base oil product that is ‘water white’. In 2012, the small hydrotreater was expanded to more than double its capacity. Sequoia carefully checked every equipment, every line and every instrument to make this expansion a success at minimum cost and little downtime.
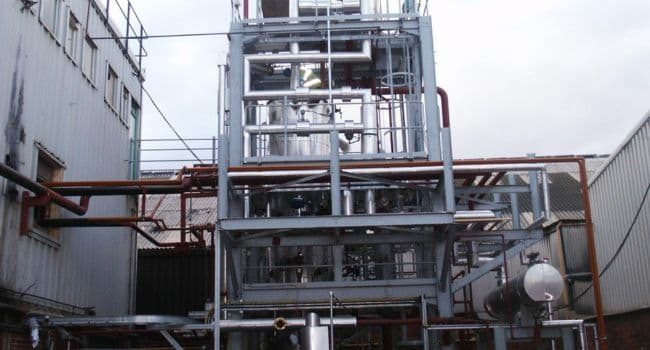
Hull, United Kingdom
Dehydration of waste fuel and oil
UK-based waste oil collector Re Group was using emulsifiers and heat to drop water out of waste lube oils and fuels. The processed oil with 0.5-1.0% water was being filtered in a centrifuge. The Hull (UK) company installed Sequoia’s efficient water evaporation equipment which produces oil with less than 0.1% water. As a result, the centrifuge works more efficiently. Ultimately, the company makes a recycled fuel oil product that easily meets government specifications for ash, Zn and water content.
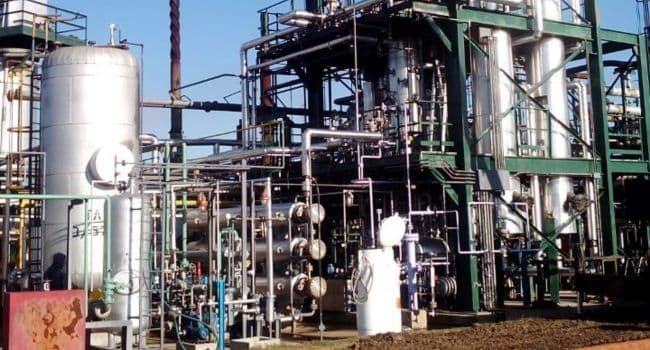
Argentina
Sequoia Hydrotreating process is operational in Argentina
Sequoia’s hydrotreating technology is operational at IASA in Argentina. This small scale hydrotreater near Buenos Aires produces 2.5 m3/hour (about 700 US gallon/hour) of Group 2 base oil from a dark distillate produced from an old furnace reboiler used for oil distillation. Sequoia has once again proven that small hydrotreaters (less than 15000 tonnes/year or 5 million gallons/year) can be built economically and operated profitably. Sequoia team worked with the customer to deal with bureaucracy and customs, as well as language barriers during design and construction. The plant was started up by 3 Sequoia engineers in under 4 weeks, starting with mechanical completion checks.